New uses for wood derived materials
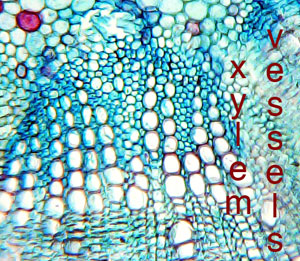
Wood is the fibrous (but porous) structural tissue found in the stems and roots of trees and shrubs. For many thousands of years, it has been used as a fuel and a construction material e.g. cruck framed barns. It is an organic material that is a mix of three different compounds:-
- Cellulose, a complex polymer (long chain molecule) made from sub-units of glucose; it makes up some 40% + of wood. Glucose is the sugar made in the leaves during photosynthesis. It can be used to make an energy storage material like starch or inulin, or the glucose units can be joined together to form long chain like molecules of cellulose.
- Hemicellulose, this is mainly composed of five-carbon sugars (e.g. xylose and mannose) that are linked in a rather irregular manner (in contrast to the order seen in cellulose). It makes up some 20% of the wood in deciduous trees, but is higher in conifers.
- Lignin (from the latin, Lignum = wood) is the third component; it is based on aromatic rings such as guaiacyl and syringyl. It makes up 25% or more of coniferous wood but the figure is a bit lower for wood from deciduous trees. Lignin is particularly important in the making of xylem vessels (or tracheids) - the water and mineral conducting tissue of trees. Lignin is resistant to decay and microbial attack; consequently,it is slow to decay and contributes to the material that results in humus in the soil.
Within the plant, the cellulose molecules / chains are linked together to make microscopic fibrils. The cell walls of all plant cells are made from cellulose micro-fibrils. These fibrils are embedded in a matrix of lignin when xylem tissue (or wood) is formed. Together they offer strength and support - enabling plants to support themselves and literally ‘grow tall’.
Wood, particularly coniferous wood, has been pulped to make paper since the mid C19th century ,but now Swedish scientists have developed a cellulose-based material that could replace oil / petroleum derived products, such as polystyrene e.g. styrofoam. A major problem with many petroleum based materials is that they degrade extremely slowly. This new product , called Cellufoam, is made using renewable and biodegradable wood-based (cellulosic) materials. This is a significant bonus for a country like Sweden, where coniferous forests are managed and continually harvested. Cellufoam was developed by Lars Wågberg, a professor in Fibre Technology at KTH Royal Institute of Technology, together with Lennart Bergström, Professor in Material Chemistry at Stockholm University, and Nicholas Tchang Cervin, a former PhD student at KTH, in the Wallenberg Wood Science Center (WWSC).
To demonstrate the potential of this new material, designers have used cellofoam in what looks like an ordinary bicycle helmet but have replaced Styrofoam with the new shock-absorbing material. The wood-based foam material offers properties comparable to Styrofoam. The production of cellufoam begins with wood cellulose fibrils, which are modified and mixed with a foaming agent, water and air (making use of a process known as Pickering stabilization).
The helmet was produced by Cellutech, a Stockholm startup that specialises in new materials made from wood, in conjunction with the Swedish Forest Industries Federation´s Ekoportal2035. The helmet is made completely from forest products. The outer layer is veneer, the straps are made from extra strong paper, and then the foam is made from cellulose fibres. Professor Wågberg believes that by using different surface treatments and other combinations with various components that flame retardant, water filtration and antibacterial materials could be developed.
Comments are closed for this post.