Sweet chestnut finger-jointing at InWood in Whitesmith,East Sussex.
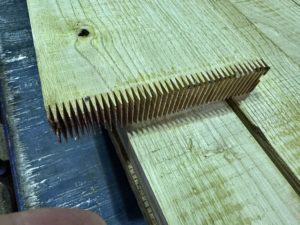
Chestnut coppice grows in abundance in the South East of England, especially in Kent and East Sussex. However it is quite small diameter, being harvested about every 15-25 years. The timber is very strong and resistant to rot. For some uses it is better than oak and unlike softwoods it does not need treating with chemicals.
The problem is how to turn these relatively thin stems into useable pieces of timber and a small company, InWood, has found an answer. I was visiting The Woodland Centre to collect a batch of six-inch decking that the factory team had made for me, and they offered me a tour round the factory. Their answer is to glue it together using finger-joints which are actually stronger than the wood itself and you can use it for decking, cladding and even structural beams. My decking boards had machined-in grooves to stop it being slippery and there were other options for width such as their three-inch or four-inch boards.
Peter Black, the factory manager, explained how they buy sweet chestnut planks and process them by sawing them to width, taking out the knots and any wood that is rotten or infested with woodworm. He says that there are also occasional shotgun pellets which need removing - many of the chestnut coppice woodlands in East Sussex are used for pheasant shoots. The sawing produces short pieces of the same width and thickness but the highlight for the visitor is seeing their German machine which automatically cuts a tooth-like pattern in each end and puts polyurethane glue on it. These sections are then pushed together to make long, virtually defect-free planks.
The factory generates plenty of waste wood which burns well and burns hot - it is either used for heating the workshop or sold for firewood. Enviously I looked at the part of the workshop where they use a huge hydraulic press to make “Gluelam”, being laminated beams from planks. These bigger timber beams have lots of advantages over the alternative of using large sections of tree trunk: the wood is much more stable, is less likely to twist & warp, longer sections can be made and there is often less wastage.
InWood’s front man is Alan Ellis whose phone number is 01825 872550, and he is happy to supply trade or retail. On their website (www.in-wood.co.uk) you can find some spectacular garden rooms which they make from laminated chestnut. We got our Sweet Chestnut decking from InWood because of the quality, and their sensible prices. This method of producing timber supports sustainable British Forestry as well as the coppicers. Successive generations of coppice workers have used their skills since at least Roman times, when sweet chestnut was first introduced to southern England.
Comments are closed for this post.
So good to hear of more domestic timber being used. Let’s hope more of our woodlands will become productive enough to supplement some of the vast amounts of timber we import from all over the globe!
Where you mentioned that it doesn’t need treating with chemicals as a softwood sometimes does, it made me think about thermowood. My local supplier in Devon has thermo spruce and also thermo-tulipwood. Both were said to have really good durability and stability and would rival something like Accoya. Would this process not open up markets for our less durable native hardwoods?. It would be great if dirty tanalising processes could be phased out (assuming thermo treatment is a cleaner process and end product).
Thanks for the article!
James
16 November, 2023